Multi-board Etching: Managing Rigid-Flex Designs and Conductivity
April 1, 2020 | Hemant Shah, Cadence Design SystemsEstimated reading time: 1 minute
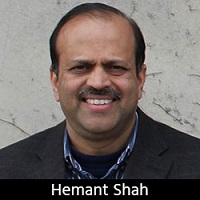
When I was a very young boy, my dad would delight and tease me by flexing his muscles. He did this with a very special flourish. Rather than simply flexing, he would put his thumb in his mouth, blow, and flex, which gave the appearance that huffing and puffing on his thumb made his bicep pop out. This was a great show for a little boy.
In PCB design, we work with a different type of flex. Advances in consumer and industrial electronic devices have allowed manufacturers to produce smaller devices that have more functionality.
Those devices use rigid-flex designs that provide the form factors needed for portability and—many times—include multiple interconnected boards. With all the interconnections between the boards, PCB designers pay equal attention to signal paths and to the electrical connectivity between boards. On the mechanical design side of things, each board must fit within an enclosure that meets the product specifications. As a result, every multi-board design combines electronic design automation (EDA) with mechanical engineering design (MCAD).
The Sum Is Greater Than the Whole
Good troubleshooting techniques involve considering a system as individual parts rather than as a whole. The same techniques apply to your work with multi-board PCB designs. Each board consists of a single unit that has its own lifecycle.
Some product designs may use a single PCB design for multiple functions or for multiple devices. Others may interconnect multiple PCB designs to produce a complete, fully functional system. Depending on the product design, a single PCB design may have multiple uses. No matter the method, the multi-design represents an overall approach to system design.
To read this entire article, which appeared in the February 2020 issue of Design007 Magazine, click here.
Suggested Items
Cadence, TSMC Collaborate on Wide-Ranging Innovations to Transform System and Semiconductor Design
04/25/2024 | Cadence Design SystemsCadence Design Systems, Inc. and TSMC have extended their longstanding collaboration by announcing a broad range of innovative technology advancements to accelerate design, including developments ranging from 3D-IC and advanced process nodes to design IP and photonics.
Ansys, TSMC Enable a Multiphysics Platform for Optics and Photonics, Addressing Needs of AI, HPC Silicon Systems
04/25/2024 | PRNewswireAnsys announced a collaboration with TSMC on multiphysics software for TSMC's Compact Universal Photonic Engines (COUPE). COUPE is a cutting-edge Silicon Photonics (SiPh) integration system and Co-Packaged Optics platform that mitigates coupling loss while significantly accelerating chip-to-chip and machine-to-machine communication.
Siemens’ Breakthrough Veloce CS Transforms Emulation and Prototyping with Three Novel Products
04/24/2024 | Siemens Digital Industries SoftwareSiemens Digital Industries Software launched the Veloce™ CS hardware-assisted verification and validation system. In a first for the EDA (Electronic Design Automation) industry, Veloce CS incorporates hardware emulation, enterprise prototyping and software prototyping and is built on two highly advanced integrated circuits (ICs) – Siemens’ new, purpose-built Crystal accelerator chip for emulation and the AMD Versal™ Premium VP1902 FPGA adaptive SoC (System-on-a-chip) for enterprise and software prototyping.
Listen Up! The Intricacies of PCB Drilling Detailed in New Podcast Episode
04/25/2024 | I-Connect007In episode 5 of the podcast series, On the Line With: Designing for Reality, Nolan Johnson and Matt Stevenson continue down the manufacturing process, this time focusing on the post-lamination drilling process for PCBs. Matt and Nolan delve into the intricacies of the PCB drilling process, highlighting the importance of hole quality, drill parameters, and design optimization to ensure smooth manufacturing. The conversation covers topics such as drill bit sizes, aspect ratios, vias, challenges in drilling, and ways to enhance efficiency in the drilling department.
Elevating PCB Design Engineering With IPC Programs
04/24/2024 | Cory Blaylock, IPCIn a monumental stride for the electronics manufacturing industry, IPC has successfully championed the recognition of the PCB Design Engineer as an official occupation by the U.S. Department of Labor (DOL). This pivotal achievement not only underscores the critical role of PCB design engineers within the technology landscape, but also marks the beginning of a transformative journey toward nurturing a robust, skilled workforce ready to propel our industry into the future.