3D Print Experts Using Ink-jet Printed Graphene
November 4, 2020 | University of NottinghamEstimated reading time: 2 minutes
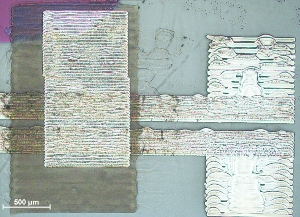
The University of Nottingham has cracked the conundrum of how to use inks to 3D-print novel electronic devices with useful properties, such as an ability to convert light into electricity.
The study shows that it is possible to jet inks, containing tiny flakes of 2D materials such as graphene, to build up and mesh together the different layers of these complex, customised structures.
Using quantum mechanical modelling, the researchers also pinpointed how electrons move through the 2D material layers, to completely understand how the ground-breaking devices can be modified in future.
The study, ‘Inter?Flake Quantum Transport of Electrons and Holes in Inkjet?Printed Graphene Devices’, has been published in the peer-reviewed journal Advanced Functional Materials.
Often described as a ‘super material’, graphene was first created in 2004. It exhibits many unique properties including being stronger than steel, highly flexible and the best conductor of electricity ever made.
Two-dimensional materials like graphene are usually made by sequentially exfoliating a single layer of carbon atoms – arranged in a flat sheet - which are then used to produce bespoke structures.
However, producing layers and combining them to make complex, sandwich-like materials has been difficult and usually required painstaking deposition of the layers one at a time and by hand.
Since its discovery, there has been an exponential growth in the number of patents involving graphene. However, in order to fully exploit its potential, scalable manufacturing techniques need to be developed.
The new paper shows that additive manufacturing - more commonly known as 3D printing - using inks, in which tiny flakes of graphene (a few billionths of a metre across) are suspended, provides a promising solution.
By combining advanced manufacturing techniques to make devices along with sophisticated ways of measuring their properties and quantum wave modelling the team worked out exactly how inkjet?printed graphene can successfully replace single layer graphene as a contact material for 2D metal semiconductors.
The study was carried out by engineers at the Centre for Additive Manufacturing and physicists at the School of Physics and Astronomy with a common interest in quantum technologies, under the £5.85m EPSRC-funded Programme Grant, Enabling Next Generation Additive Manufacturing.
The researchers used a wide range of characterisation techniques - including micro?Raman spectroscopy (laser scanning), thermal gravity analysis, a novel 3D orbiSIMS instrument and electrical measurements - to provide detailed structural and functional understanding of inkjet?printed graphene polymers, and the effects of heat treating (annealing) on performance.
The next steps for the research are to better control the deposition of the flakes by using polymers to influence the way they arrange and align and trying different inks with a range of flake sizes. The researchers also hope to develop more sophisticated computer simulations of the materials and the way they work together, developing ways of mass-manufacturing they devices they prototype.
The University of Nottingham is a research-intensive university with a proud heritage, consistently ranked among the world's top 100. Studying at the University of Nottingham is a life-changing experience and we pride ourselves on unlocking the potential of our students. We have a pioneering spirit, expressed in the vision of our founder Sir Jesse Boot, which has seen us lead the way in establishing campuses in China and Malaysia - part of a globally connected network of education, research and industrial engagement.
Read the original article here.
Suggested Items
Real Time with… IPC APEX EXPO 2024: Tools, Training, and Trends in Manufacturing Engineering
04/25/2024 | Real Time with...IPC APEX EXPOGuest Editor Kelly Dack and Product Specialist Erik Bateham of Polar Instruments discuss Polar's latest technology, including their role in aiding manufacturing engineers. They highlight the advanced capabilities of Polar's tools and the critical role of signal integrity analysis, as well as the importance of accurate modeling in board manufacturing. Polar's unique training approach and demonstration contact details are also explored.
TTM Celebrates the Grand Opening of Its First Manufacturing Facility in Penang
04/25/2024 | TTM Technologies, Inc.TTM Technologies, Inc., a leading global manufacturer of technology solutions including mission systems, radio frequency (RF) components and RF microwave/microelectronic assemblies, and quick-turn and technologically advanced printed circuit boards (PCBs), officially opened its first manufacturing plant in Penang, Malaysia with an investment of USD200 million (approximately RM958 million).
Listen Up! The Intricacies of PCB Drilling Detailed in New Podcast Episode
04/25/2024 | I-Connect007In episode 5 of the podcast series, On the Line With: Designing for Reality, Nolan Johnson and Matt Stevenson continue down the manufacturing process, this time focusing on the post-lamination drilling process for PCBs. Matt and Nolan delve into the intricacies of the PCB drilling process, highlighting the importance of hole quality, drill parameters, and design optimization to ensure smooth manufacturing. The conversation covers topics such as drill bit sizes, aspect ratios, vias, challenges in drilling, and ways to enhance efficiency in the drilling department.
Elevating PCB Design Engineering With IPC Programs
04/24/2024 | Cory Blaylock, IPCIn a monumental stride for the electronics manufacturing industry, IPC has successfully championed the recognition of the PCB Design Engineer as an official occupation by the U.S. Department of Labor (DOL). This pivotal achievement not only underscores the critical role of PCB design engineers within the technology landscape, but also marks the beginning of a transformative journey toward nurturing a robust, skilled workforce ready to propel our industry into the future.
Fujitsu, METRON Collaborate to Drive ESG Success
04/24/2024 | JCN NewswireFujitsu Limited and METRON SAS, a French cleantech company specializing in energy management solutions for industrial decarbonization, today announced a strategic initiative to contribute to the realization of carbon neutrality in the manufacturing industry.